Alcast Company Fundamentals Explained
Alcast Company Fundamentals Explained
Blog Article
6 Simple Techniques For Alcast Company
Table of ContentsAlcast Company Fundamentals ExplainedThe 4-Minute Rule for Alcast CompanySee This Report about Alcast CompanyThe Single Strategy To Use For Alcast CompanyExamine This Report about Alcast CompanyAbout Alcast Company
The subtle difference lies in the chemical material. Chemical Contrast of Cast Aluminum Alloys Silicon promotes castability by lowering the alloy's melting temperature level and enhancing fluidness throughout spreading. It plays a crucial function in permitting elaborate molds to be loaded accurately. Additionally, silicon adds to the alloy's stamina and use resistance, making it useful in applications where durability is important, such as vehicle components and engine components.It also boosts the machinability of the alloy, making it simpler to process right into finished products. In this means, iron adds to the overall workability of light weight aluminum alloys. Copper increases electric conductivity, making it advantageous in electric applications. It also enhances corrosion resistance and includes in the alloy's general stamina.
Manganese adds to the stamina of aluminum alloys and boosts workability (aluminum casting manufacturer). It is typically made use of in wrought light weight aluminum items like sheets, extrusions, and profiles. The existence of manganese help in the alloy's formability and resistance to splitting during fabrication procedures. Magnesium is a light-weight element that gives stamina and influence resistance to aluminum alloys.
The Only Guide for Alcast Company
It allows the production of lightweight elements with exceptional mechanical residential or commercial properties. Zinc boosts the castability of light weight aluminum alloys and aids control the solidification process throughout spreading. It improves the alloy's toughness and firmness. It is usually located in applications where complex forms and fine details are required, such as decorative spreadings and particular auto parts.
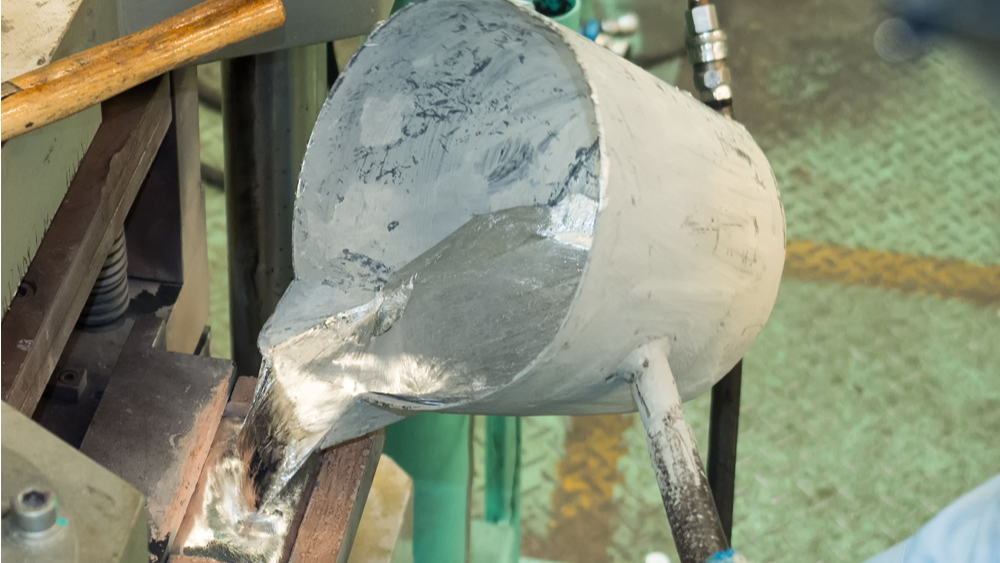
The main thermal conductivity, tensile toughness, yield strength, and elongation differ. Amongst the above alloys, A356 has the highest thermal conductivity, and A380 and ADC12 have the most affordable.
Facts About Alcast Company Uncovered

In precision spreading, 6063 is appropriate for applications where complex geometries and premium surface area coatings are paramount. Instances include telecommunication units, where the alloy's exceptional formability enables sleek and cosmetically pleasing styles while preserving structural stability. In a similar way, in the Lighting Solutions industry, precision-cast 6063 parts create stylish and effective lighting fixtures that call for elaborate forms and excellent thermal efficiency.
The A360 displays remarkable prolongation, making it suitable for complicated and thin-walled elements. In precision spreading applications, A360 is well-suited for sectors such as Customer Electronics, Telecommunication, and Power Tools.
Examine This Report about Alcast Company
Its unique residential or commercial properties make A360 a beneficial choice for precision spreading in these sectors, enhancing product longevity and high quality. Aluminum alloy 380, or A380, is an extensively used spreading alloy with numerous distinct qualities. It uses superb castability, making it an optimal option for accuracy spreading. A380 shows good fluidity when molten, making sure detailed and detailed molds are accurately recreated.
In precision spreading, light weight aluminum 413 shines in the Customer Electronics and Power Tools sectors. This alloy's click here for more exceptional corrosion resistance makes it a superb option for exterior applications, ensuring lasting, sturdy products in the pointed out industries.
The Facts About Alcast Company Revealed
The aluminum alloy you choose will substantially affect both the casting process and the residential properties of the last item. Because of this, you must make your decision carefully and take an informed approach.
Identifying the most suitable aluminum alloy for your application will certainly suggest considering a vast selection of features. These relative alloy attributes comply with the North American Die Casting Organization's standards, and we've divided them right into 2 classifications. The very first category addresses alloy characteristics that influence the production process. The second covers features impacting the residential properties of the end product.
Not known Factual Statements About Alcast Company
The alloy you pick for die casting straight affects a number of facets of the casting procedure, like how simple the alloy is to deal with and if it is prone to casting issues. Hot splitting, additionally referred to as solidification breaking, is a regular die casting flaw for light weight aluminum alloys that can result in interior or surface-level rips or cracks.
Specific light weight aluminum alloys are more vulnerable to warm fracturing than others, and your selection ought to consider this. An additional usual defect discovered in the die spreading of light weight aluminum is pass away soldering, which is when the cast stays with the die walls and makes ejection hard. It can harm both the actors and the die, so you should search for alloys with high anti-soldering properties.
Rust resistance, which is already a remarkable attribute of light weight aluminum, can differ substantially from alloy to alloy and is an important characteristic to consider depending on the environmental problems your item will certainly be subjected to (Foundry). Wear resistance is another home frequently sought in aluminum items and can separate some alloys
Report this page